It’s a good thing that people nowadays are becoming aware of the adverse effects of plastic use. But what’s even better is that more people are now translating this awareness into concrete actions. Sure, ditching single-use plastic bottles, plastic packaging, and straws is a major step. But what about existing plastic waste?
Well, we’ve seen sneakers made out of recycled ocean plastic. This time, Scotland-based company MacRebur has found a new way to repurpose plastic waste by incorporating them into asphalt mixes. And the result? Pothole-free roads that are stronger and last longer.
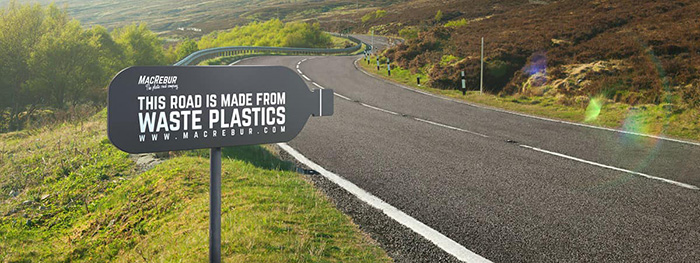
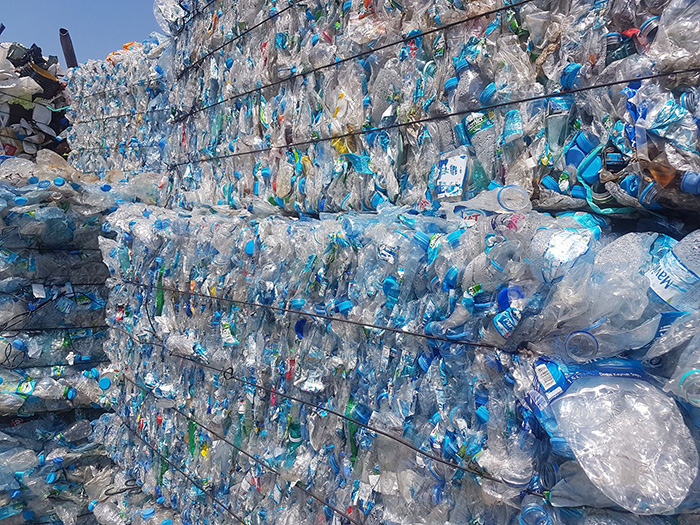
Company CEO and engineer Toby McCartney revealed that there were two things that inspired him to set up his company. The first one was his daughter’s concern over the alarming amount of plastic waste in the oceans. As a father, he doesn’t hope for his daughter to grow up in a world with waste-filled bodies of water. The second one was a trip to India where he witnessed the locals burning plastic waste and filling them into potholes.
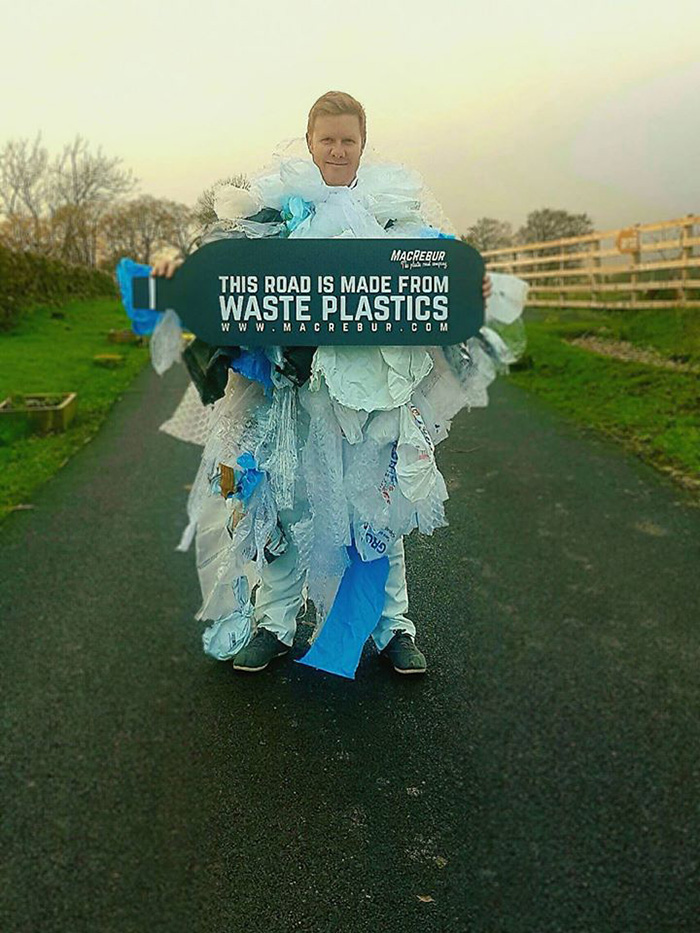
However, McCartney knew that the latter would not sit well with the councils in the UK. This meant that he had to figure out an eco-friendlier way of implementing it. So, he got together with his friends, Gordon Redi and Nick Burnett, and launched MacRebur in April 2016. Together, they looked into innovative ways to make the use of plastic waste for road construction possible.
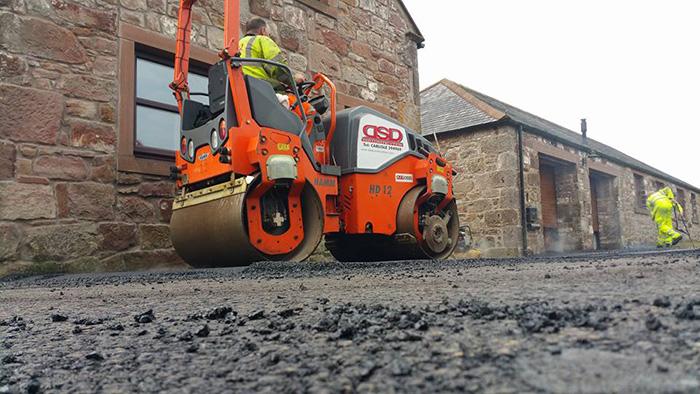
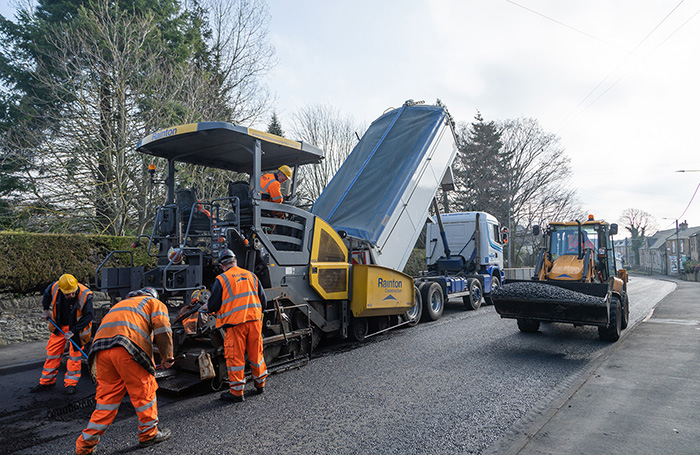
The company takes pride in constructing “plastic roads” and aims to help solve two world problems. These include plastic waste problems and poor road quality.
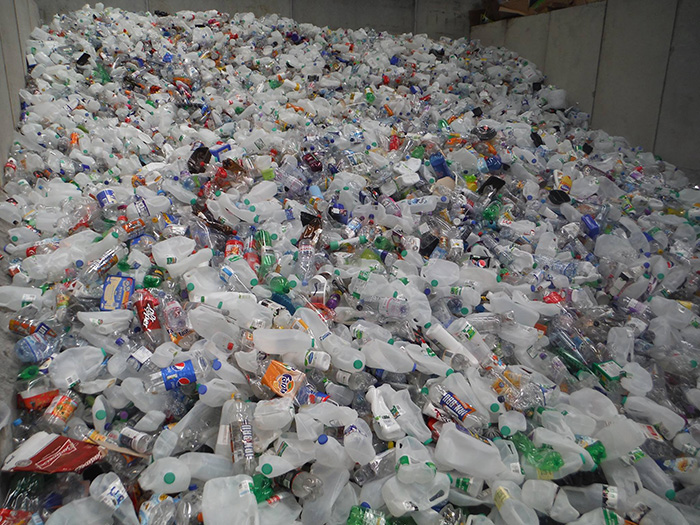
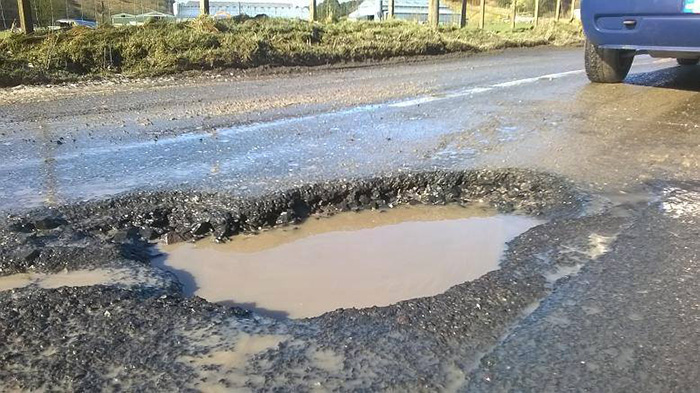
By integrating plastic bottle waste into asphalt mixes for road construction, the company addresses both of these concerns at once
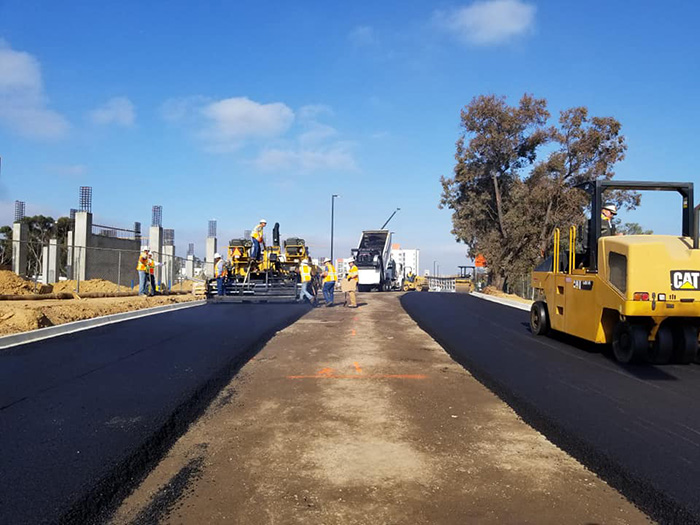
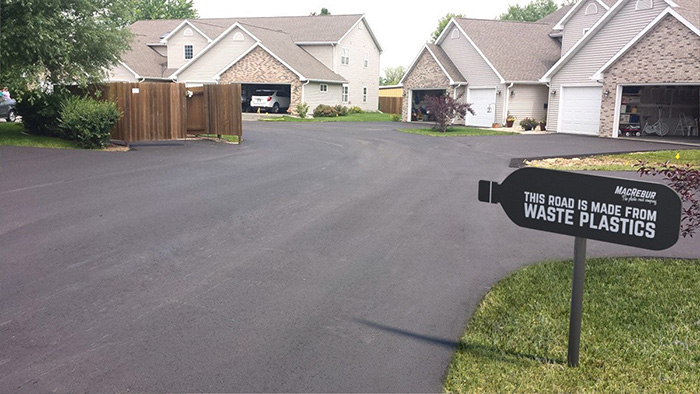
The company starts by collecting plastic waste from both household and commercial use—40% household and 60% commercial. Afterward, they use a granulator to turn this chunk of waste into small pellets of no more than 5mm. They then mix these plastic pellets with a “secret” activator. The company claims is what “makes the plastic bind properly” into roads.
“Our activator is patented and what’s in it is a secret! This blend of plastic granules and the activator–let’s call it the MacRebur mix–then goes to an asphalt producer.”
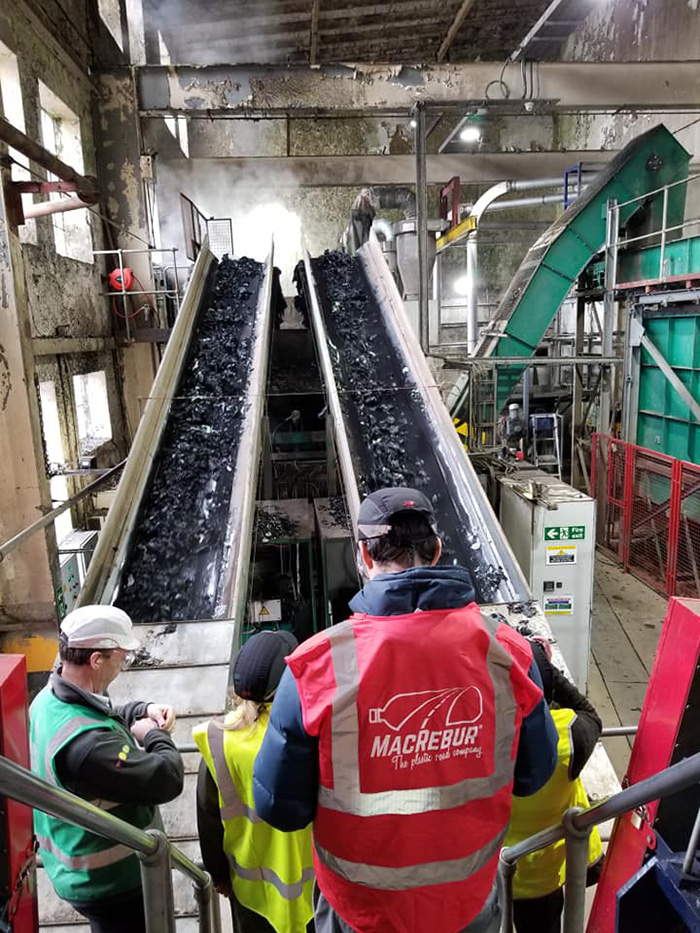
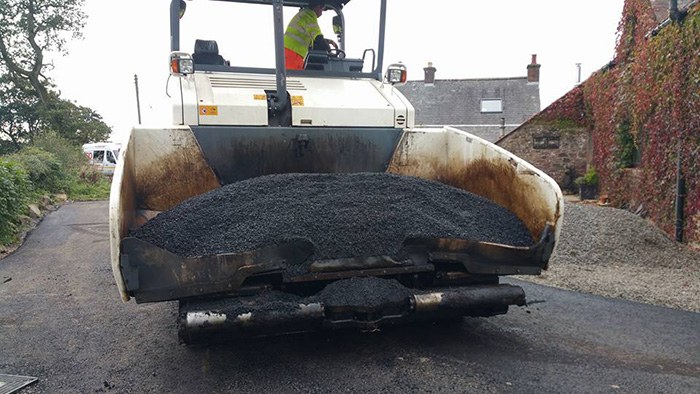
Roads generally consist of around 90% limestones, rocks, and sand, and around 10% bitumen. Bitumen is a mixture that binds all these components together. So, technically, MacRebur’s technology replaces a significant portion of the bitumen. As such, this results in a reduction of carbon footprint and enhancement of asphalt performance at the same time.
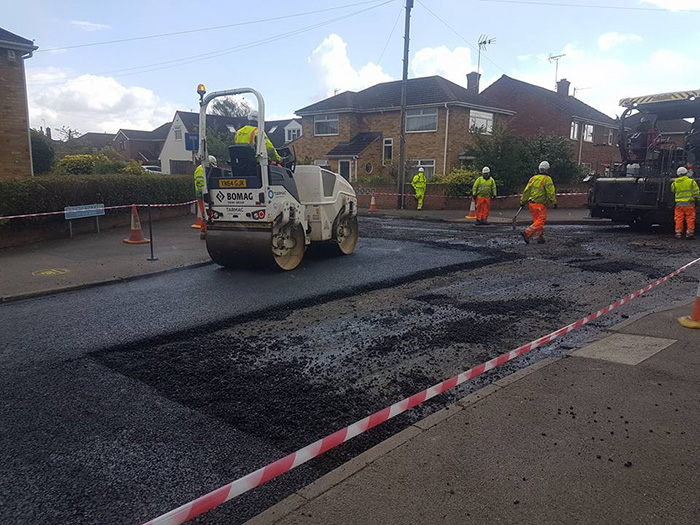
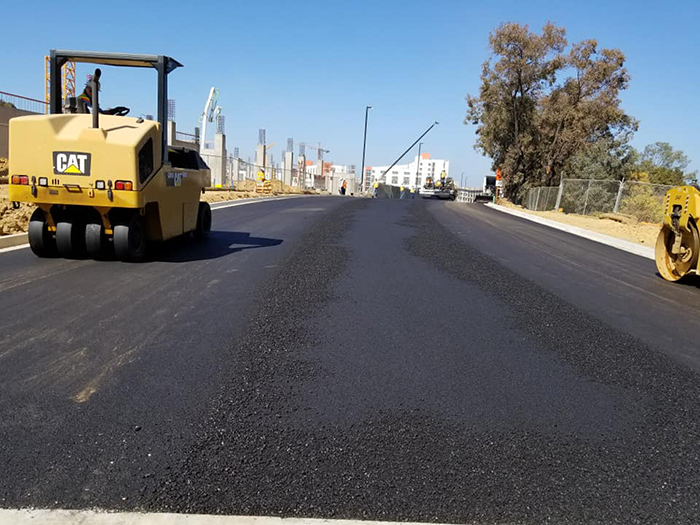
Since these roads contain plastic, the company claims that they’re more flexible. As such, they perform better than regular asphalt, especially under contraction and expansion brought about by weather change. In addition, they’re less prone to potholes and cracks, which makes them a more sustainable alternative overall. So, it’s not surprising that McCartney still considers plastic a “great product” in general.
“At the end of the day, plastic is a great product. It lasts for long, which is a problem if it’s a waste product, but not a problem if we want it to last.”
Here’s what people have to say about MacRebur’s effort to repurpose plastic waste
Witness how MacRebur incorporates plastic bottle waste into road construction via the videos below
Source: MacRebur Website | Facebook